Nuevas formas de acero para vehículos más fuertes y livianos
Los fabricantes de automóviles están modificando los procesos de producción para crear una serie de nuevos aceros con las propiedades adecuadas que les permitan fabricar automóviles que sean más seguros y eficientes en el consumo de combustible.
Manténgase informado
Suscríbase al boletín de noticias de Knowable en español
Al igual que muchas innovaciones útiles, la creación de acero de alta calidad por metalúrgicos indios hace más de dos mil años puede haber sido una feliz confluencia de mano de obra inteligente y suerte.
La cocción de trozos de hierro con carbón vegetal en un recipiente especial de arcilla produjo algo completamente nuevo, que los indios llamaron wootz. Los ejércitos romanos no tardaron en utilizar espadas de acero wootz para aterrorizar y someter a las tribus salvajes y peludas de la antigua Europa.
Veinticuatro siglos después, los fabricantes de automóviles recurren a hornos de arco eléctrico, máquinas de estampado caliente y procesos de temple y separación que los antiguos jamás habrían imaginado. Estos métodos están dando lugar a nuevas formas de perfeccionar el acero para proteger los blandos cuerpos humanos cuando los vehículos chocan entre sí, como inevitablemente ocurre, al tiempo que se reduce el peso de los automóviles para reducir su nocivo impacto en el planeta.
“Es una revolución”, afirma Alan Taub, profesor de ingeniería de la Universidad de Michigan que lleva muchos años en el sector. Los nuevos aceros, docenas de variedades y subiendo, combinados con polímeros ligeros e interiores y estructuras hechas de fibras de carbono, recuerdan los embriagadores días de principios del siglo pasado cuando, dice, “Detroit era Silicon Valley”.
Estos materiales pueden reducir el peso de un vehículo en cientos de kilos —y cada kilo perdido de peso ahorra unos 3 dólares en combustible a lo largo de la vida útil del vehículo, por lo que la rentabilidad es difícil de negar—. La nueva máxima, dice Taub, es “el material adecuado en el lugar adecuado”.
La transición a los vehículos de batería subraya la importancia de estos nuevos materiales. Puede que los vehículos eléctricos no contaminen, pero son pesados: el Volvo XC40 Recharge, por ejemplo, pesa un 33 % más que la versión de gasolina (y pesaría aún más si el acero que rodea a los pasajeros fuera tan voluminoso como solía serlo). Pesado puede ser peligroso.
“La seguridad, especialmente cuando se trata de nuevas políticas de transporte y nuevas tecnologías, no puede pasarse por alto”, dijo Jennifer Homendy, jefa de la Junta Nacional de Seguridad en el Transporte, al Consejo de Investigación del Transporte en 2023. Además, reducir el peso de un vehículo eléctrico en un 10 % supone una mejora de la autonomía de aproximadamente un 14 %.
Todavía en los años sesenta, la jaula de acero que rodeaba a los pasajeros era de lo que los fabricantes de automóviles llaman acero blando. El blindaje del Jurásico de Detroit no era muy diferente del que Henry Ford había introducido décadas antes. Era pesado y era abundante.
Con la publicación en 1965 del libro de Ralph Nader Unsafe at Any Speed: The Designed-In Dangers of the American Automobile (Inseguro a cualquier velocidad: los peligros intrínsecos del automóvil americano), los grandes fabricantes de automóviles se dieron cuenta de que ya no podían perseguir exclusivamente la velocidad y el rendimiento. Los embargos petroleros de los años setenta solo aceleraron el ritmo del cambio: el acero de los automóviles tenía que ser más resistente y ligero, y consumir menos combustible.
En respuesta, en los últimos 60 años, como los chefs que manejan una máquina sous vide para producir el bocado perfecto, los fabricantes de acero —sus hornos de arco que alcanzan miles de grados Fahrenheit, con robots que se encargan de la cocción— han creado una gran variedad de aceros para satisfacer todas las necesidades. Hay aceros endurecidos de alta resistencia para el chasis; aceros inoxidables resistentes a la corrosión para los paneles laterales y el techo; y metales muy elásticos en los parachoques para absorber los impactos sin arrugarse.
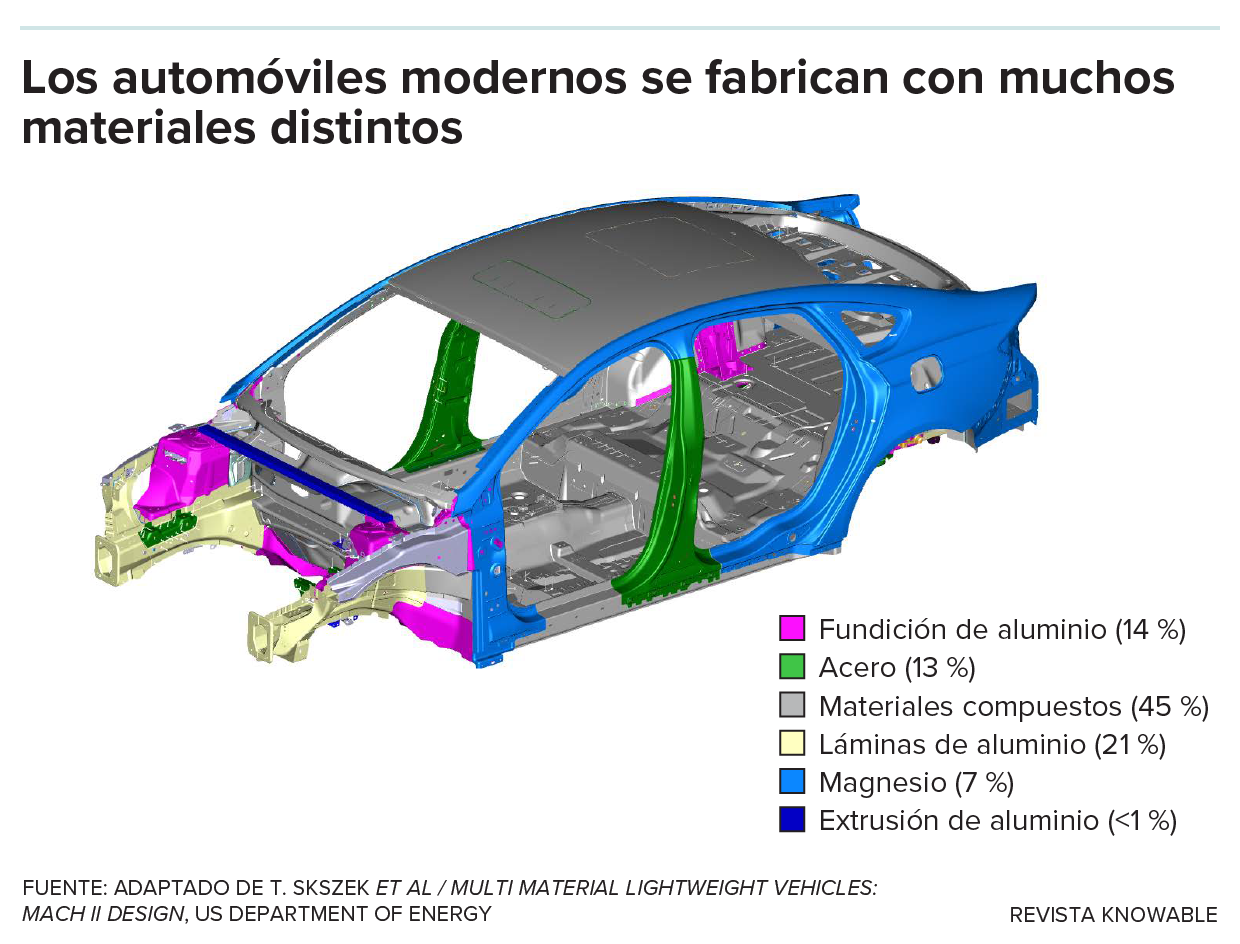
Los fabricantes de automóviles utilizan una amplia gama de materiales para construir la carrocería de un vehículo, eligiendo el que mejor se adapta a cada aplicación.
Trucos con el acero
La mayor parte del acero tiene más de un 98 % de hierro. La diferencia la marcan los porcentajes restantes —que a veces son solo centésimas en el caso de los metales añadidos para conferir las propiedades deseadas—. Igual de importantes son los métodos de tratamiento: el calentamiento, el enfriamiento y la transformación, como el laminado de las chapas antes de conformar las piezas. Cada modificación, a veces de solo unos segundos, cambia la estructura del metal y le confiere propiedades diferentes. “Se trata de jugar con el acero”, dice John Speer, director del Centro de Investigación de Productos y Procesado Avanzado del Acero de la Escuela de Minas de Colorado.
En el nivel más básico, las propiedades del acero tienen que ver con la microestructura: la disposición de los distintos tipos, o fases, de acero en el metal. Algunas fases son más duras, mientras que otras confieren ductilidad, una medida de cuánto puede doblarse y retorcerse el metal sin que se rompa y cree bordes dentados que penetran y rasgan los blandos cuerpos humanos. A nivel atómico, existen principalmente cuatro fases en el acero para automóviles, entre ellas la más dura y quebradiza, denominada martensita, y la más dúctil, la austenita. Los fabricantes de automóviles pueden variar estas fases manipulando los tiempos y las temperaturas del proceso de calentamiento para obtener las propiedades que desean.
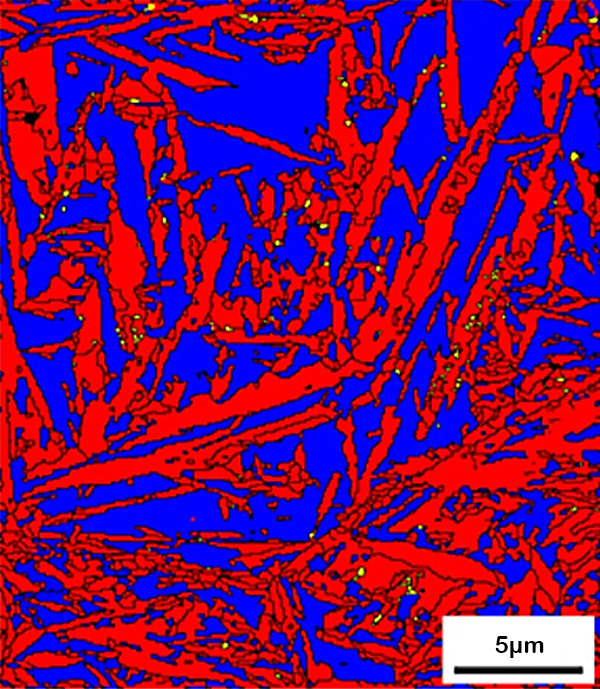
Esta micrografía electrónica de una muestra de acero muestra dos tipos o fases diferentes de acero: la austenita, más blanda y trabajable (azul), y la martensita, más dura y quebradiza (rojo). Los siderúrgicos pueden variar la mezcla de ambas modificando la forma de calentar y enfriar una pieza de acero.
CRÉDITO: ADAPTADO DE R. HOSSAIN ET AL / SCIENTIFIC REPORTS 2016
Investigadores académicos y fabricantes de acero, en estrecha colaboración con los fabricantes de automóviles, han desarrollado tres generaciones de lo que ahora se denomina acero avanzado de alta resistencia. La primera, adoptada en los años noventa y aún muy utilizada, combinaba bien resistencia y ductilidad. Una segunda generación utilizó aleaciones más exóticas para lograr una ductilidad aún mayor, pero esos aceros resultaron caros y difíciles de fabricar.
La tercera generación, que según Speer está empezando a llegar a las fábricas, utiliza técnicas de calentamiento y enfriamiento para producir aceros más resistentes y moldeables que los de primera generación; casi diez veces más resistentes que los aceros comunes del pasado; y mucho más baratos (aunque menos dúctiles) que los de segunda generación.
Los fabricantes de acero han aprendido que el tiempo de enfriamiento es un factor crítico para crear la disposición final de los átomos y, por tanto, las propiedades del acero. El enfriamiento más rápido, conocido como temple, congela y estabiliza la estructura interna antes de que sufra más cambios durante las horas o días que podría tardar en alcanzar la temperatura ambiente.
Uno de los tipos más resistentes de acero para automóviles modernos —utilizado en los componentes estructurales más críticos, como paneles laterales y pilares— se fabrica sobrecalentando el metal con boro y manganeso a una temperatura superior a 850 grados Celsius. Tras volverse maleable, el acero se transfiere en 10 segundos a una matriz, o forma, donde se da forma a la pieza y se enfría rápidamente.
En una versión de lo que se conoce como plasticidad inducida por transformación, el acero se calienta a una temperatura alta, se enfría a una temperatura más baja y se mantiene así durante un tiempo para, a continuación, enfriarse rápidamente. Esto produce islas de austenita rodeadas por una matriz de ferrita más blanda, con regiones de bainita y martensita más duras. Este acero puede absorber una gran cantidad de energía sin fracturarse, lo que lo hace útil en parachoques y pilares.
Las recetas pueden ajustarse aún más mediante el uso de diversas aleaciones. Henry Ford empleaba aleaciones de acero y vanadio hace más de un siglo para mejorar el rendimiento del acero en su Modelo T, y las recetas de aleación siguen mejorando hoy en día. Un ejemplo moderno del uso de metales más ligeros en combinación con el acero es el camión F-150 de Ford Motor Company, fabricado en aluminio, cuya versión de 2015 pesa casi 317 kilos menos que el modelo anterior.
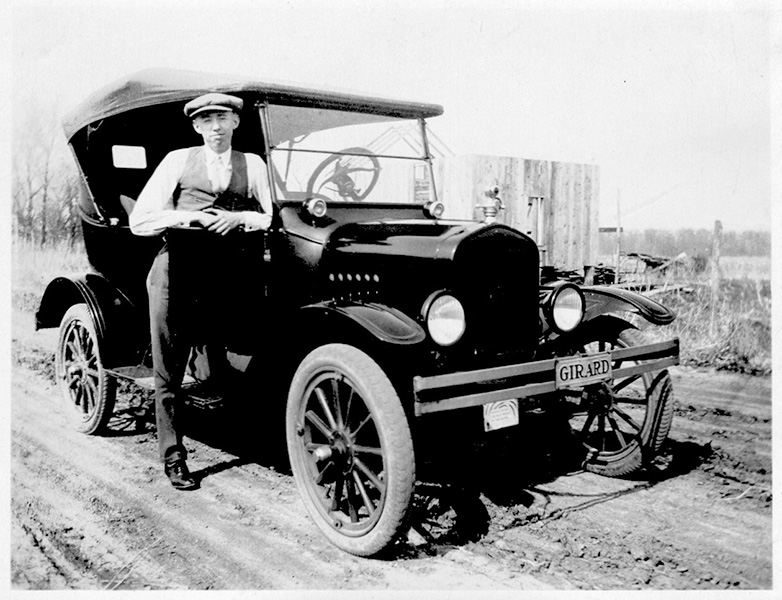
Las sofisticadas aleaciones de acero tienen una larga historia. Incluso en las primeras décadas del siglo XX, Henry Ford añadía el elemento vanadio al acero que utilizaba para construir el Modelo T.
CRÉDITO: JOHN TEWELL / FLICKR
Un proceso utilizado junto con los nuevos materiales es el hidroconformado de tubos, en el que un metal se dobla en formas complejas mediante la inyección a alta presión de agua u otros fluidos en un tubo, expandiéndolo en la forma de una matriz circundante. Esto permite fabricar piezas sin soldar dos mitades, lo que ahorra tiempo y dinero. El larguero del bastidor de aluminio de un Corvette, la pieza hidroformada más grande del mundo, ahorra un 20 % de masa con respecto al larguero de acero que sustituyó, señala Taub, coautor de un artículo sobre aligeramiento en automoción publicado en 2019 en el Annual Review of Materials Research.
Nuevas aleaciones
Más recientes introducciones son las aleaciones de titanio y, sobre todo, las de niobio, que aumentan la resistencia al estabilizar la microestructura del metal. En un artículo de 2022, Speer calificó la introducción del niobio de “uno de los avances más importantes de la metalurgia física del siglo XX”.
Una herramienta que ahora acorta la distancia entre ensayo y error es la computadora. “La idea es utilizar la computadora para desarrollar materiales más rápidamente que mediante la experimentación”, afirma Speer. Ahora es posible probar nuevas ideas hasta el nivel atómico sin necesidad de inclinarse sobre la mesa de trabajo o encender un horno.
La incesante búsqueda de mejores materiales y procesos llevó al ingeniero Raymond Boeman y sus colegas a fundar en 2015 el Institute for Advanced Composites Manufacturing Innovation (Instituto para la Innovación en la Fabricación de Compuestos Avanzados, IACMI), con una subvención federal de 70 millones de dólares, es un lugar donde la industria puede desarrollar, probar y ampliar nuevos procesos y productos.
“El campo está evolucionando en muchos sentidos”, afirma Boeman, que ahora dirige la investigación del instituto sobre la ampliación de estos procesos. El IACMI ha estado trabajando en la búsqueda de sustitutos más respetuosos con el clima para plásticos convencionales como el polipropileno, ampliamente utilizado. En 1960, se incorporaban menos de 45 kilos de plástico al vehículo típico. En 2017, la cifra había aumentado a casi 160 kilos, porque el plástico es barato de fabricar y tiene una alta relación resistencia-peso, lo que lo hace ideal para los fabricantes de automóviles que intentan ahorrar peso.
En 2019, según Taub, entre el 10 % y el 15 % de un vehículo común estaba hecho de polímeros y materiales compuestos, desde los componentes de los asientos hasta los maleteros, las piezas de las puertas y los tableros de mando. Y cuando esos automóviles llegan al final de su vida útil, sus plásticos y otros materiales difíciles de reciclar, conocidos como residuos de trituradoras de automóviles —5 millones de toneladas de residuos— acaban en los vertederos o, lo que es peor, en el medio ambiente en general.
Investigadores se esfuerzan actualmente por desarrollar plásticos más resistentes, ligeros y ecológicos. Al mismo tiempo, los nuevos productos de fibra de carbono permiten utilizar estos materiales ligeros incluso en lugares de carga, como los bajos estructurales, reduciendo aún más la cantidad de metales pesados utilizados en las carrocerías.
Está claro que queda trabajo por hacer para que los automóviles sean menos peligrosos, tanto para el cuerpo humano como para el planeta que recorren a diario tanto por trabajo y como por diversión. Pero Taub se muestra optimista sobre el futuro de Detroit y la capacidad de la industria para resolver los problemas que surgieron con el fin de la época de los coches de caballos. “Les digo a los estudiantes que tendrán trabajo seguro durante mucho tiempo”.
Artículo traducido por Debbie Ponchner
10.1146/knowable-090524-1
Apoye a la revista Knowable
Ayúdenos a hacer que el conocimiento científico sea accesible para todos
DONAREXPLORE MÁS | Lea artículos científicos relacionados