Hacia un plástico verdaderamente compostable
Los científicos de materiales están elaborando polímeros respetuosos con el ambiente a partir de fuentes naturales como la seda, las fibras vegetales y algas. Los costos y la aceptación siguen siendo obstáculos por superar.
Manténgase informado
Suscríbase al boletín de noticias de Knowable en español
Fue aclamado como algo maravilloso: durante el boom del petróleo en los años cincuenta, los químicos empezaron a convertir los residuos que salían de las refinerías en plástico —empaques de plástico, muebles de plástico, fibras de plástico tejidas en telas sintéticas—. Eran materiales milagrosos, moldeables y flexibles, pero resistentes y duraderos. Desde entonces, la producción mundial de plástico se ha disparado: el ser humano ha creado 8.000 millones de toneladas métricas de plástico.
Decir que ese auge ha traído problemas es quedarse corto. Más de la mitad del plástico que se ha producido —unas 5.000 millones de toneladas métricas— yace esparcido por la superficie de la Tierra. Cada día, más de 10.000 toneladas de plástico llegan a los océanos. La durabilidad del plástico, una de las propiedades que hacen que este material sea tan milagroso, lo ha convertido en un potente contaminante.
Para ser justos con los primeros promotores, los plásticos han cambiado el mundo. Muchas tecnologías esenciales —desde los vehículos de motor hasta los teléfonos celulares y las computadoras— utilizan plástico. La espuma aislante ha contribuido a que las casas sean 200 veces más eficientes desde el punto de vista energético. Las películas de plástico prolongan la vida útil de los alimentos perecederos.
“No me gusta cómo la gente demoniza el plástico como si fuera la cosa más malvada que jamás hemos hecho”, dice Eleftheria Roumeli, física de la Universidad de Washington y coautora de un repaso sobre polímeros sostenibles en el Annual Review of Materials Research de 2023. “Es producto de una ingeniería brillante”.
En lugar de abandonar este material, piensa, tenemos que encontrar una mejor y más amable versión: polímeros con la resistencia a la tracción y la flexibilidad de los plásticos modernos que procedan de fuentes biológicas sostenibles y puedan devolverse eficazmente al medio ambiente.
Esto significa replantearse la producción de plástico desde cero.
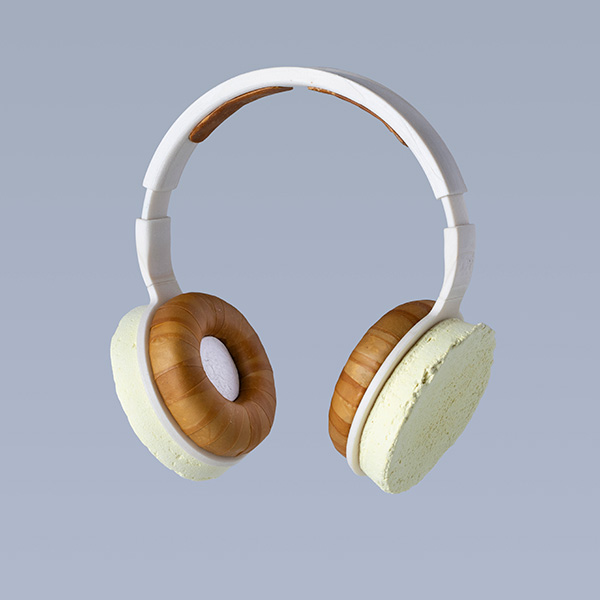
En 2019, una colaboración científica experimental llamada Korvaa produjo lo que llamaron “los primeros auriculares cultivados por microbios del mundo”. El proyecto requería una serie de materiales, algunos rígidos, otros similares a la espuma y otros similares a la tela, todos de origen biológico.
CRÉDITO: AIVAN
Del monómero al polímero
El enfoque actual de la producción de plásticos consiste en dos grandes pasos: primero una ruptura y luego una reconstrucción.
La descomposición — “craqueo”, como se conoce, realizado a alta temperatura y presión— convierte los materiales refinados del petróleo en moléculas simples conocidas como monómeros. Estos se convierten en la columna vertebral del producto que se vuelve a fabricar. Las cadenas o entramados resultantes se conocen como polímeros y son el componente estructural básico de cualquier plástico.
Pero el plástico aún no está acabado. Después viene la incorporación de aditivos: colorantes, retardantes de llama y rellenos. Los científicos de materiales tienen en cuenta una gran variedad de variables, desde la “dureza” a la “resistencia al desgarro” o el “módulo de tracción”, que indican cómo se comporta un plástico ante distintos tipos de tensiones. Los aditivos más importantes ajustan estas propiedades, generalmente modificando los enlaces entre las cadenas poliméricas. Los productos químicos conocidos como plastificantes, por ejemplo, se incrustan entre las cadenas, ayudando a aumentar la flexibilidad —pero, como contrapartida, haciendo que el plástico sea más fácil de romper—.
Mezclando y combinando polímeros y aditivos, los químicos crean los materiales compuestos finales que se utilizan en envoltorios de alimentos y botellas de refrescos, como microesferas en cosméticos, incluso como los hidrogeles flexibles que, en forma de lentes de contacto, adherimos a nuestras córneas para agudizar la vista. Gracias a la química, un solo polímero como el cloruro de polivinilo —o PVC, como se conoce comúnmente— puede convertirse en tuberías rígidas para aguas pluviales o en prendas de vestir.
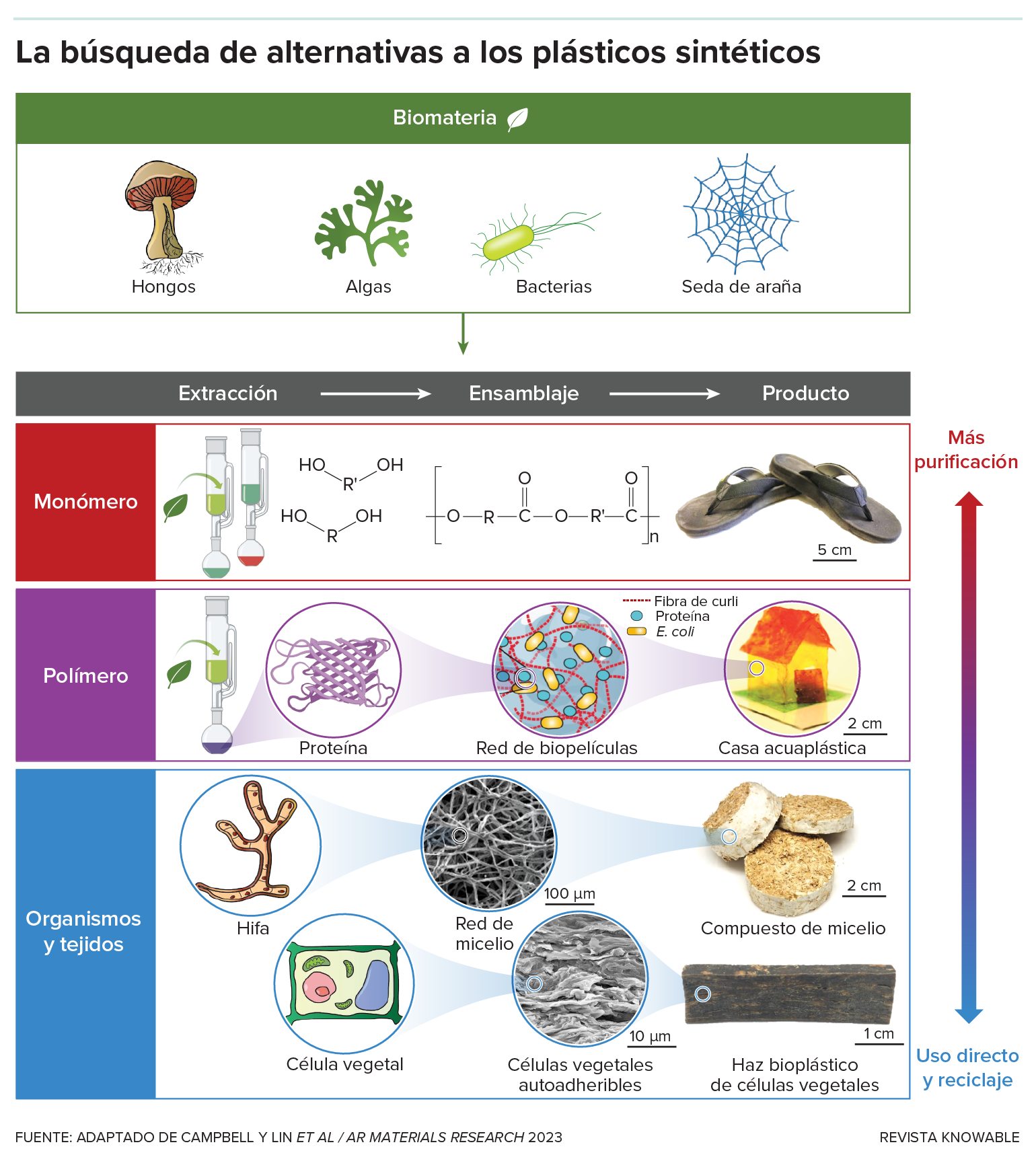
Los investigadores estudian cómo producir monómeros y polímeros a partir de biomateria y cómo utilizar organismos y tejidos enteros como materia prima. Las unidades de materia prima más pequeñas, como los monómeros, requieren más procesamiento, pero son más fáciles de utilizar en las instalaciones de producción existentes.
La producción de plásticos representa hasta el 8 % del consumo mundial de combustibles fósiles —cifra que podría aumentar, según una estimación, hasta el 20 % en 2050—. Pero los químicos ya creaban plásticos “sintéticos” décadas antes de que despegara la industria petrolera, a partir, entre otros materiales, de residuos de cáscaras de avena y aceite vegetal. Una de las vías hacia plásticos más sostenibles es volver a esas fuentes biológicas.
En 2006, por ejemplo, la empresa petroquímica brasileña Braskem puso en marcha experimentos para ver si podían transformar de forma económica el azúcar en etileno, el monómero más importante en la producción de plásticos básicos. En 2010, Braskem ya vendía un plástico de polietileno “totalmente biológico”, o bio-PE.
La gran ventaja de este material es que la caña de azúcar captura carbono de la atmósfera a medida que crece. Y como, estructuralmente hablando, el bio-PE es indistinguible de su gemelo sintético, el bio-PE ha sido fácil de desplegar en aplicaciones como el envasado de alimentos, cosméticos y juguetes.
Pero ser químicamente indistinguible también es un problema. Como el polietileno no aparece en entornos naturales, pocos microbios han desarrollado la capacidad de romper sus enlaces moleculares. Por tanto, el bio-PE no resuelve el problema de los residuos. En otras palabras, que algo sea un “bioplástico” no significa que sea intrínsecamente sostenible.
“Ninguno de estos términos está suficientemente regulado o definido de forma significativa, lo que provoca una gran confusión”, afirma Rachel Meidl, investigadora en energía y sostenibilidad del Instituto Baker de la Universidad Rice.
Meidl clasifica los plásticos y sus posibles sustitutos en cuatro cuadrantes. Un eje indica el origen de los materiales: algunos son de base biológica, mientras que otros son derivados del petróleo. El otro eje traza el destino final: algunos materiales son biodegradables y otros no. Pero incluso un material que se sitúe en el mejor de estos cuadrantes —tanto de base biológica como biodegradable— no es necesariamente una panacea. Ser biodegradable solo significa que un material puede ser descompuesto por microbios, aunque el resultado sean pequeños trozos de microplásticos. Los materiales ideales no solo son biodegradables, sino también compostables —una categoría más restringida que indica que el material puede descomponerse en componentes orgánicos inocuos para plantas y animales—.
Por desgracia, la compostabilidad no es fácil de conseguir. Es casi seguro que haya encontrado ácido poliláctico, o PLA, en forma de cubiertos compostables y envases de comida para llevar. El PLA, el plástico de base biológica más común, es técnicamente compostable, pero en condiciones específicas que solo se obtienen en instalaciones industriales que aún no existen en número suficiente. Como la mayoría de los envases de PLA para llevar acaban desechados junto con los restos de comida, los compostadores tienen que perder el tiempo separándolos.
Una forma de mejorar los plásticos podría ser buscar mejores monómeros de origen biológico. En 2020, un equipo de científicos de California reportó que había aislado un tipo de monómero llamado poliol a partir de aceites producidos por algas, y luego lo volvió a ensamblar en un plástico similar a la espuma que podría utilizarse en calzado comercial. El material se degradó eficazmente cuando se depositó en el suelo.
Sin embargo, algunos científicos creen que la mejor opción es dejar atrás el proceso estándar de descomposición en monómeros y posterior reconstrucción, que consume mucha energía. Según David Kaplan, ingeniero biomédico de la Universidad de Tufts, la naturaleza ya ofrece polímeros prometedores que son compostables. Y como se degradan en escalas de tiempo diferentes, si se selecciona el polímero adecuado o se ajusta correctamente, se pueden crear materiales que se adapten a aplicaciones variadas.
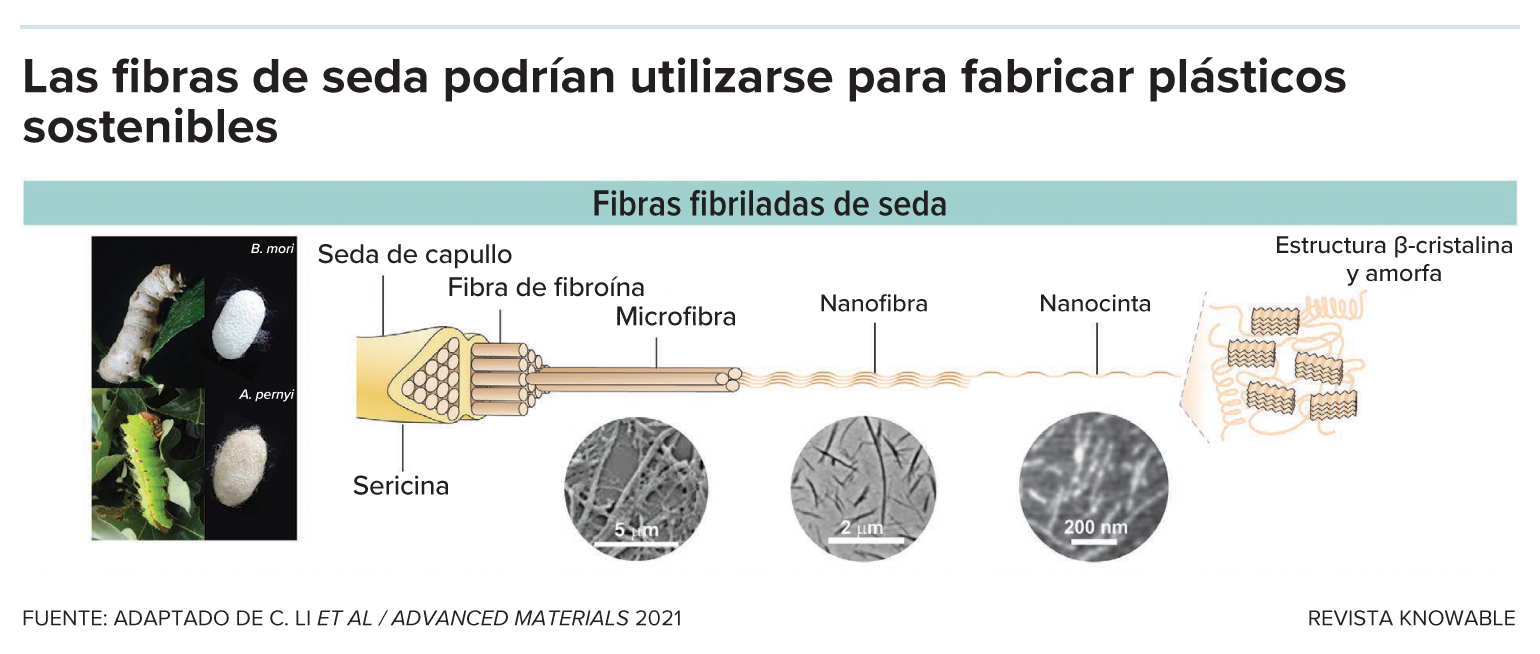
Algunas biofibras, como la celulosa y la seda (en la imagen), tienen una estructura jerárquica, en la que las fibras microscópicas se agrupan en capas cada vez más grandes. Estas moléculas tienen enlaces débiles, pero los enlaces son de alta densidad, un atributo potencialmente útil para aplicaciones humanas.
Consideremos la celulosa, el polímero biológico más común, presente en las paredes celulares de las plantas. Se trata esencialmente de una cadena de moléculas de azúcar, pero estas cadenas se ensamblan en pequeños hilos llamados nanofibrillas, que se agrupan en microfibras y luego en las grandes fibras que son visibles, como las hebras fibrosas del apio, por ejemplo. Los científicos de materiales llaman a esto estructura jerárquica.
Los polímeros sintéticos, por el contrario, se prensan en una tolva y se extruden hasta formar un glóbulo homogéneo. El resultado es “enlaces fuertes y duros” entre moléculas, afirma Kaplan. “La biología no hace mucho de eso”. En su lugar, los biopolímeros presentan enlaces mucho más débiles —normalmente interacciones electrostáticas que unen los átomos de hidrógeno de una molécula polimérica con los de otra, pero a densidades muy altas—.
Pero si se comprenden mejor estas estructuras, los ingenieros podrán mejorar los materiales biológicos. La investigación ha demostrado, por ejemplo, que cuanto más fina es una fibra de celulosa, mayor es su resistencia a la tracción, lo que significa que el material resiste la rotura bajo tensión. Al aumentar la superficie, los átomos de hidrógeno están mejor situados para crear y romper dinámicamente enlaces entre cadenas contiguas.
Ir directamente a las células
Una vez que se ha renunciado a los monómeros —eliminando todo un paso en el proceso de producción del plástico— ¿por qué no ir más allá? Algunos científicos de materiales persiguen lo que Kaplan denomina “diseño de abajo hacia arriba”: en lugar de aislar y rehacer biopolímeros individuales, utilizan lo que la naturaleza les ha proporcionado — creando materiales bioplásticos a partir de células enteras u otros materiales biológicos, sin necesidad de romperlos ni extraerlos—.
Roumeli, por ejemplo, ha explotado la promesa de las células de algas. Son pequeñas y, por tanto, fácilmente manipulables; contienen grandes cantidades de proteínas, que son polímeros biológicos, además de otros materiales útiles. Ella y sus estudiantes tomaron algas en polvo y las pasaron por una prensadora en caliente. Tras varias pruebas en las que variaron el tiempo de prensado, la temperatura y la cantidad de presión aplicada —todo lo cual afecta a la forma en que se unen las moléculas—, descubrieron que podían producir un material más resistente que muchos plásticos básicos.
El material también era reciclable: se podía volver a moler y prensar. (Las pruebas demostraron que el material perdía algo de resistencia con cada generación de reciclado, lo que también ocurre con los plásticos sintéticos). Si se arrojara descuidadamente a la tierra, el material se rompería a la misma velocidad que una cáscara de banano.
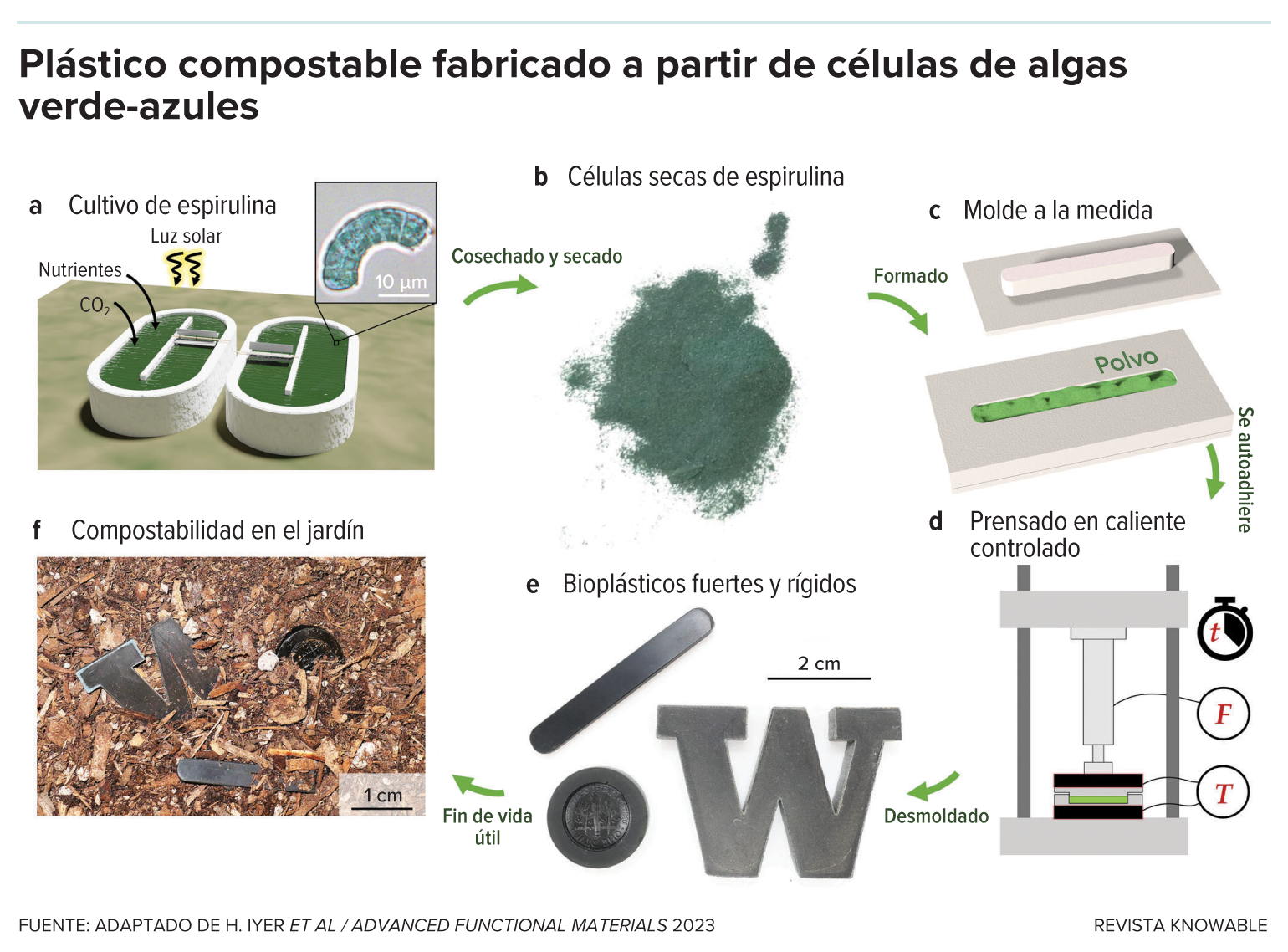
Investigadores de la Universidad de Washington prensan con calor células de un alga verde-azul llamada espirulina para obtener un bioplástico más resistente de lo necesario para muchas aplicaciones humanas y que puede compostarse fácilmente en los patios de las casas.
Kaplan ha realizado trabajos similares con seda, que durante mucho tiempo se consideró demasiado frágil para ser procesada térmicamente. Se pensaba que los enlaces de hidrógeno se romperían con el calor y la seda simplemente se quemaría. Sin embargo, en un artículo publicado en 2020, Kaplan y sus colegas demostraron que los gránulos de seda podían moldearse, como el plástico, en un material afinable. Desde entonces, ha descubierto que se pueden procesar capullos enteros de esta forma.
Según Roumeli, con estos materiales todos ganamos. Son renovables, no utilizan combustibles fósiles y pueden absorber el carbono atmosférico mientras crecen. Podrían biodegradarse por completo. “Donde no son una victoria es en nuestra economía —y nuestra escalabilidad—”, afirma.
Este es quizá el mayor problema de este nuevo enfoque de los plásticos: su naturaleza radical significa que va a ser caro, al menos por ahora. Para que un producto sea barato, hay que poder producirlo en instalaciones ya existentes, ya que eso ayuda a una nueva empresa a evitar importantes costos de capital. Pero los propietarios de esas instalaciones pueden considerar los compuestos biológicos demasiado impuros —como “basura”—, dice Gadi Rothenberg, químico del Instituto Van ‘t Hoff de Ciencias Moleculares de la Universidad de Ámsterdam.
Rothenberg señala que, en la materia prima utilizada para producir tereftalato de polietileno, el plástico empleado en las botellas de gaseosas, solo una molécula de cada 100.000 es distinta del monómero deseado. Los materiales biológicos rara vez son tan puros.
También es posible que los fabricantes prefieran lo probado a lo inesperado. Rothenberg desarrolló su propio polímero sostenible a base de plantas, que pensó que se parecía lo suficiente a los materiales estándar como para ser una opción fácil de utilizar en la producción de muebles. Pero cuando lo presentó por primera vez a las empresas, “al principio no querían ni oír hablar de él”, dice. Incluso el bio-PE, un producto a base de caña de azúcar químicamente idéntico a su pariente sintético, tiene un costo de fabricación 30 % más caro, según algunas cifras, por lo que las empresas preocupadas por los resultados se van a quedar con el producto tradicional.
En la actualidad, los plásticos de origen biológico representan menos del 1 % del mercado, según la asociación comercial Plastics Europe. El impulso a los polímeros de origen biológico “no llegará a ninguna parte hasta que no se equipare en los aspectos económicos”, afirma Rothenberg. En última instancia, predice, los gobiernos tendrán que reconocer el costo real y total del plástico tradicional —su huella de carbono y los gastos derivados de la limpieza de la contaminación— antes de que se impongan materiales más sostenibles.
Sin embargo, los científicos de vanguardia se muestran esperanzados. Roumeli señala que el polietileno sintético —“el plástico más barato, más producido y más consumido que tenemos hoy en día”— fue en su día una novedad. Kaplan dice que no duda de que algún día “todos estos precursores y polímeros se fabricarán biológicamente, o con verdadera circularidad en mente”.
“Pero aún no hemos llegado a ese punto”, añade. El problema es que, con la acumulación de residuos plásticos y el aumento de las temperaturas, puede que no tengamos mucho tiempo para esperar.
Artículo traducido por Debbie Ponchner
10.1146/knowable-040424-1
Apoye a la revista Knowable
Ayúdenos a hacer que el conocimiento científico sea accesible para todos
DONAREXPLORE MÁS | Lea artículos científicos relacionados